Na última matéria vimos como funciona o serviço de flushing com óleo. Dessa vez, veremos quais são os objetivos da manutenção preditiva.
As indústrias e prestadores de serviço estão sempre buscando qual a modalidade de manutenção preditiva mais adequada e capaz de gerar os melhores níveis de disponibilidade, vida útil e produtividade de seus equipamentos.
Nos últimos anos, o desenvolvimento das técnicas de monitoramento e análise do desempenho e condições dos equipamentos mostra que a manutenção preditiva é a melhor alternativa possível para essas empresas.
Neste post, vamos discutir quais os tipos de manutenção existentes, bem como os métodos e objetivos da manutenção preditiva e suas vantagens em relação aos outros tipos de manutenção tradicionalmente aplicados.
Os Tipos de Manutenção
Desde as primeiras plantas industriais, a manutenção mais comumente adotada sempre foi a corretiva. Seu princípio é bastante simples: uma peça ou um equipamento quebrado é reparado. Nesse contexto, não há nenhum gasto contínuo com manutenção, até que a máquina apresente falhas e seja necessária a mobilização de equipes de manutenção, compra de componentes e paradas de manutenção. Isso acaba gerando custos muito elevados, exigindo alta disponibilidade do estoque de peças e, muitas vezes, a parada do equipamento defeituoso, o que prejudica o desempenho da produção.
Confira abaixo os tipos de manutenção mais comuns a serem aplicados e como eles se distinguem dos processos da manutenção preditiva:
Manutenção Preventiva
Dentre os tipos de manutenção, a manutenção preventiva se destaca por manter o nível dos equipamentos, programando intervenções periódicas para reduzir a deterioração dos equipamentos. Essa manutenção preventiva combina os métodos com base no tempo e nas condições para manter o equipamento funcionando.
A partir das intervenções, essa consegue assegurar o desempenho dos materiais estruturais, prevenindo a corrosão, a fadiga e outras formas de deterioração. Um fator importante da manutenção preventiva é que a inspeção ou a intervenção no equipamento é feita periodicamente, mesmo que ele não apresente problemas.
Manutenção de Parada
A manutenção de parada, também conhecida como “manutenção por melhoria” ou “prevenção de manutenção”, consiste em paradas de equipamentos com o objetivo de fazer com que esses atinjam o estado novamente. Na manutenção de parada, revisões e reparos são feitos em todos os itens, com o intuito de assegurar, com alta probabilidade, um bom desempenho do equipamento por um longo período de tempo.
Manutenção Corretiva
Conforme apresentado anteriormente, a manutenção corretiva é a forma mais comum e mais primária de manutenção. Muitas vezes é associada ao ciclo de “quebra-repara”. Contudo, é aplicada não apenas quando há efetivamente uma falha ou pane (a “quebra” propriamente dita).
Qualquer defeito que ainda não evoluiu para a falha pode disparar o processo de intervenção. Se aplicada isoladamente, a Corretiva é uma das formas mais caras e custosas de manutenção, proporcionando baixa utilização das cadeias produtivas, diminuição da vida útil dos equipamentos e paradas completas em momentos inadequados.
Manutenção de Quebra
Indo na contramão aos tipos de manutenção planejados, a manutenção de quebra está entre aqueles onde não há nenhum planejamento de atividades. Isso significa que o objetivo é deixar o equipamento operar até que falhe (entre em pane), para então ser consertado.
A manutenção de quebra somente pode ser aplicada quando as falhas não afetam significativamente a operação, a produção ou não geram nenhuma perda financeira ou de segurança ou dano ao meio ambiente.
Manutenção Baseada no Tempo
A manutenção baseada no tempo se resume em inspeção visual, lubrificação, limpeza do equipamento e na substituição de peças para prevenir falhas repentinas e problemas de processo. Este tipo de manutenção geralmente não é complexo, sem exigir especialização, podendo ser realizado pelos próprios operadores após um treinamento básico. A manutenção baseada no tempo faz parte das atividades de manutenção autônoma e da manutenção especializada.
Manutenção Baseada nas Condições
Diferente da manutenção baseada no tempo, a manutenção baseada nas condições é desencadeada pelas condições reais do equipamento mais do que pela passagem de um intervalo de tempo predeterminado. A principal ferramenta empregada neste caso é a manutenção preditiva, e ela consiste em coletar e reportar informações que se baseiam em certos valores conhecidos dos equipamentos. Alguns exemplos são: coleta da temperatura através de termografia, análise da vibração pela utilização de acelerômetros e análise da qualidade do óleo em laboratórios.
Com o monitoramento constante, é possível intervir nos equipamentos assim que as variações são detectadas, de forma a corrigir os desvios antes que o equipamento quebre. Este tipo de manutenção exige conhecimentos técnicos avançados da equipe e geralmente é terceirizado por empresas especialistas em cada segmento.
Manutenção Preditiva: o que é e Como é Feita
A manutenção preditiva está dentro da filosofia da manutenção baseada nas condições.
Mas vai além, tendo como premissa programar intervenções nas máquinas, baseadas em indicadores dos próprios equipamentos. Esses dados são fornecidos por um programa de monitoramento e inspeções de desempenho. São comumente avaliados fatores como vibração, termografia e outros.
Os principais objetivos da manutenção preditiva consistem em determinar antecipadamente a necessidade de serviços de manutenção, eliminar desmontagens desnecessárias para inspeção e aumentar o tempo de disponibilidade dos equipamentos.
Tal metodologia ainda visa reduzir o trabalho de emergência não planejado, impedir o aumento dos danos e aproveitar a vida útil total dos componentes. Dessa forma, sua aplicação permite aumentar o grau de confiança no desempenho de um equipamento ou na linha de produção e determinar previamente as interrupções de fabricação para cuidar dos equipamentos que precisam passar por manutenção.
Execução da Manutenção Preditiva
A execução da manutenção preditiva é realizada com a utilização de instrumentos adequados, capazes de registrar fenômenos, tais como:
- Vibração nas máquinas
- Variação de pressão
- Variação de temperatura
- Partículas de desgaste ou contaminação
Após a constatação e o conhecimento do fenômeno. São adotados dois procedimentos: diagnóstico e análise da tendência da falha que pode ocorrer. Detectada a irregularidade, o responsável terá o encargo de estabelecer, na medida do possível, um diagnóstico referente à origem e à gravidade do defeito constatado. Esse diagnóstico deve ser feito antes de se programar o reparo.
A análise da tendência da falha consiste em prever com antecedência a avaria ou a quebra. Por meio de instrumentos que exerçam vigilância constante, predizendo a necessidade do reparo. Seus métodos de investigação visam apurar informações referentes ao estudo das vibrações, análise de óleo, análise do estado das superfícies e análises estruturais de peças.
Nesse cenário, ganha especial importância a análise de óleo como ferramenta da manutenção preditiva.
Manutenção Preditiva: Análise de Óleo
Estudos permanentes e detalhados dos óleos lubrificantes utilizados nas máquinas podem apontar para anomalias. Os níveis de desgaste de componentes, por exemplo, muitas vezes são identificados pela presença de micropartículas no óleo. Contaminações por água ou combustíveis ou outros produtos também podem ser constatadas pela análise de óleo. Esse monitoramento pode orientar ações pontuais de manutenção antecipada, prevenindo falhas futuras.
A análise de óleo é aplicada com o objetivo de promover a economia de lubrificantes e evitar defeitos nos equipamentos. Em sua aplicação, são monitoradas as condições de desgaste da máquina, as propriedades dos óleos e seu grau de contaminação.
Confira algumas das determinações mais importantes logo abaixo:
- Metais por espectrometria de emissão atômica (desgaste, aditivação e contaminação)
- Viscosidade (qualidade do óleo, contaminação por outros produtos)
- Índice de acidez (TAN) (degradação)
- Índice de basicidade (TBN) (degradação)
- Contagem de partículas (contaminação)
- Teor de água (contaminação)
- Espectrometria de Infravermelho: Oxidação, Sulfatação, Nitração e Fuligem (degradação e contaminação)
- Ferrografia (desgaste e contaminação)
- Índice PQ (desgaste)
Alguns dos instrumentos mais comuns nos processos laboratoriais são os espectrômetros, viscosímetros, tituladores, contadores e microscópios. Com essas ferramentas, as análises vão definir a necessidade e a periodicidade das intervenções na máquina e/ou no próprio lubrificante.
Manutenção Preditiva: Redução de Custos
Sempre aconselhamos as empresas que para aumentar a vida útil de seus equipamentos. E reduzir custos precisam estar em dia com a manutenção preditiva de seu maquinário. Avaliar as condições desses equipamentos requer um trabalho minucioso de coleta e análise de dados dos equipamentos monitorados.
O foco da manutenção preditiva está sempre na redução de custos e na maior disponibilidade do equipamento. As ferramentas que compõem o processo da manutenção preditiva, auxiliam a detectar anomalias nos equipamentos, como seu estado de desgaste. Além de informar a presença de qualquer substância contaminante em diversos componentes. Desse modo, a manutenção preditiva possibilita que algo seja feito antes que os defeitos se agravem, evitando prejuízos maiores.
A manutenção preditiva possibilita que ações possam ser tomadas no momento certo. Evitando desgaste dos equipamentos ou perda de algum componente importante em decorrência de alguma falha não identificada ou prevenida. Isso ainda proporciona que o maquinário esteja sempre pronto para ser usado e funcionando com total capacidade, para mais produtividade. O que aumenta a confiança nos equipamentos.
Conclusão
Nesta postagem, buscamos compartilhar algumas informações que mostram a importância da manutenção preditiva para aproveitar o melhor dos seus equipamentos. Consequentemente, influenciar positivamente a sua produção. Essa gestão é uma maneira inteligente e eficiente de se obter mais disponibilidade e confiabilidade dos ativos.
Basicamente, podemos dizer que as máquinas “conversam” conosco.
As técnicas de manutenção preditiva permitem ao especialista “ouvir”, traduzir e interpretar as informações que as máquinas nos passam. A partir daí, atuar para obter delas o máximo aproveitamento, a melhor disponibilidade, com o menor custo e maior confiabilidade.
Realizar manutenções regulares pode fazer toda a diferença na produtividade de suas máquinas. Otimize sua cadeia produtiva.
Fonte: Manutenção Preditiva
Serviço de Análise e Filtragem de Óleo, Limpeza Química / Decapagem e Flushing para Todo o Brasil
Para serviços de filtragem, desidratação e análise de óleo, flushing, limpeza química, teste hidrostático e outros, que visem a manutenção preventiva, preditiva e corretiva da sua empresa, contrate a Filtrovali. Estamos situados em Itajaí / Santa Catarina e atendemos todo o Brasil.
Estamos alinhados com o mercado, tendo uma frota própria e equipamentos de última geração. Nossa equipe é altamente qualificada, possuindo todas as certificações para prestar todo o serviço com segurança.
Quando o assunto é manutenção e redução de custos, nós entramos em ação. Com uma estrutura sólida, tecnologia, experiência no que faz, a Filtrovali cresce dia após dia atuando nos mais diversos seguimentos, tais como: estaleiros, usinas hidrelétricas, portos, siderurgia, petroquímica e indústria em geral.
Solicite um orçamento, sem compromisso, através do formulário abaixo. Teremos o maior prazer em lhe atender!
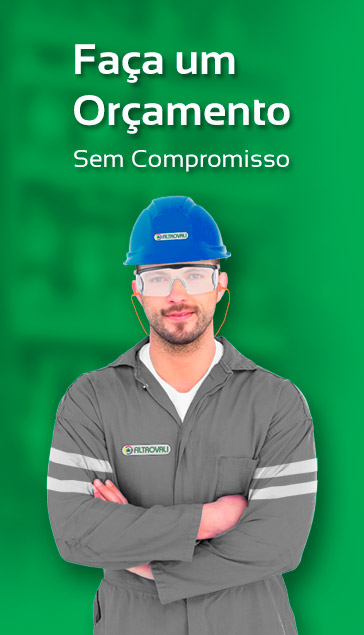